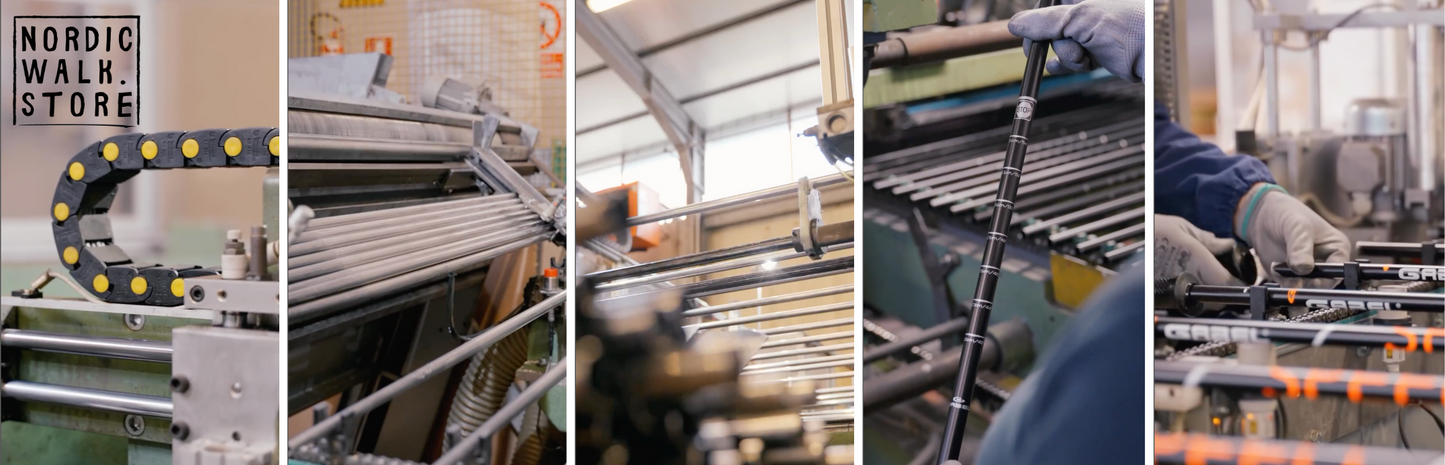
The right poles are the one bit of essential kit for enjoying Nordic Walking. But have you ever wondered how these poles are made? From selecting the right materials to the final touches, the manufacturing process is a fascinating blend of science and craftsmanship. Let's take a closer look!
1. It’s all in the season
In the UK, Nordic Walking is an all-year-round activity, but in Italy, Finland and Germany, the homes of Gabel, Exel and Leki, manufacturers class it as a spring/summer activity. In the run up to winter the factories are busy making ski poles and then through the winter the walking pole manufacture begins, ready for stock release in Spring.
At Nordic Walk Store, we have to plan well in advance, often booking our stock up to a year ahead. Our main delivery of poles arrives in March and April, which means by January and February, we may start running low on certain colours, lengths, and styles. Spring is also when travel poles become available, but once they sell out, they’re often not restocked until the following year. By August, our stock begins to run low again as we wait for the limited restock in September, ready for autumn and Christmas sales, but after that, we’re back to waiting for the next spring delivery.
This cycle means planning your purchase early is key to getting your preferred style and size. If you’re looking for specific colours or travel poles, keep an eye out for the spring drop to avoid disappointment!
2. Choosing the Right Materials
The journey of a Nordic walking pole begins with selecting the right materials. Durability, weight, and comfort are crucial factors. Common materials used include:
- Aluminum: Known for its strength and lightweight properties, aluminum poles are durable and budget-friendly
- Carbon Fiber: High-end poles often use carbon fiber for its superior strength-to-weight ratio, reducing vibration for a more comfortable nordic wal
- Composite Materials: Some poles combine carbon and fiberglass to balance cost, durability, and performance.
2. Cutting and Shaping the Shaft
Once the material is chosen, the manufacturing process begins by cutting the raw tubes to the desired length. Advanced machinery ensures precision, maintaining uniformity across all poles. The tubes are then shaped to the ergonomic design needed for optimal performance.
3. Reinforcement and Coating
To enhance durability and resistance to wear and tear, the poles undergo reinforcement and coating processes:
- Heat Treatment: Strengthens the material, making it resilient to bending and breaking.
- Protective Coating: A layer of protective paint or anodizing is applied, which prevents corrosion and adds an appealing finish.
4. Grip and Strap Assembly
The grip and strap are crucial for comfort and efficiency during use.
- Grips: Typically made of cork, or rubber provide a comfortable and anti-slip hold. Cork is popular for its moisture-wicking properties. A mold is typically used to produce grips and they are secured to the shafts using hot glue, allowing for retrofitting new grips later on in the pole’s life.
- Straps: Designed to fit securely around the wrist, allowing users to push off efficiently without tightly gripping the pole. High-quality straps are made of breathable, durable materials.
5. Adding the Tip
The tip of a Nordic walking pole is designed for optimal traction and versatility:
- Carbide Tips: Durable and designed for off-road terrains like dirt trails and rocky surface.
- Rubber Pads: Detachable pads are added for Nordic walking on hard surfaces like pavement, reducing noise and impact.
Tips are replaceable, just like grips and straps, keeping your poles fit for purpose for miles and miles.
6. Quality Control and Testing
Before hitting the market, each pole undergoes rigorous testing to ensure durability, flexibility, and user safety. This includes:
- Stress Testing: Checking resistance to bending and breaking under pressure.
- Grip and Strap Comfort Tests: Ensuring ergonomic design and secure fit.
- Field Testing: Real-world testing by athletes and Nordic walking enthusiasts for feedback and final adjustments.
Conclusion
The manufacturing of Nordic walking poles involves precision, high-quality materials, and a deep understanding of user needs. Whether you're a beginner or an experienced Nordic walker, knowing the craftsmanship behind your poles can enhance your appreciation for this powerful fitness tool.
Riccardo Bizzotto from Italian brand Gabel SRL puts it nicely:
"At Gabel we do our best to limit the impact on the environment, because a well made product, designed to last and be serviced when needed, is way less impactful than a cheaper product with a short lifespan"
Ready to try out a pair? Explore our collection of expertly crafted Nordic walking poles designed for performance and comfort. Happy Nordic walking!